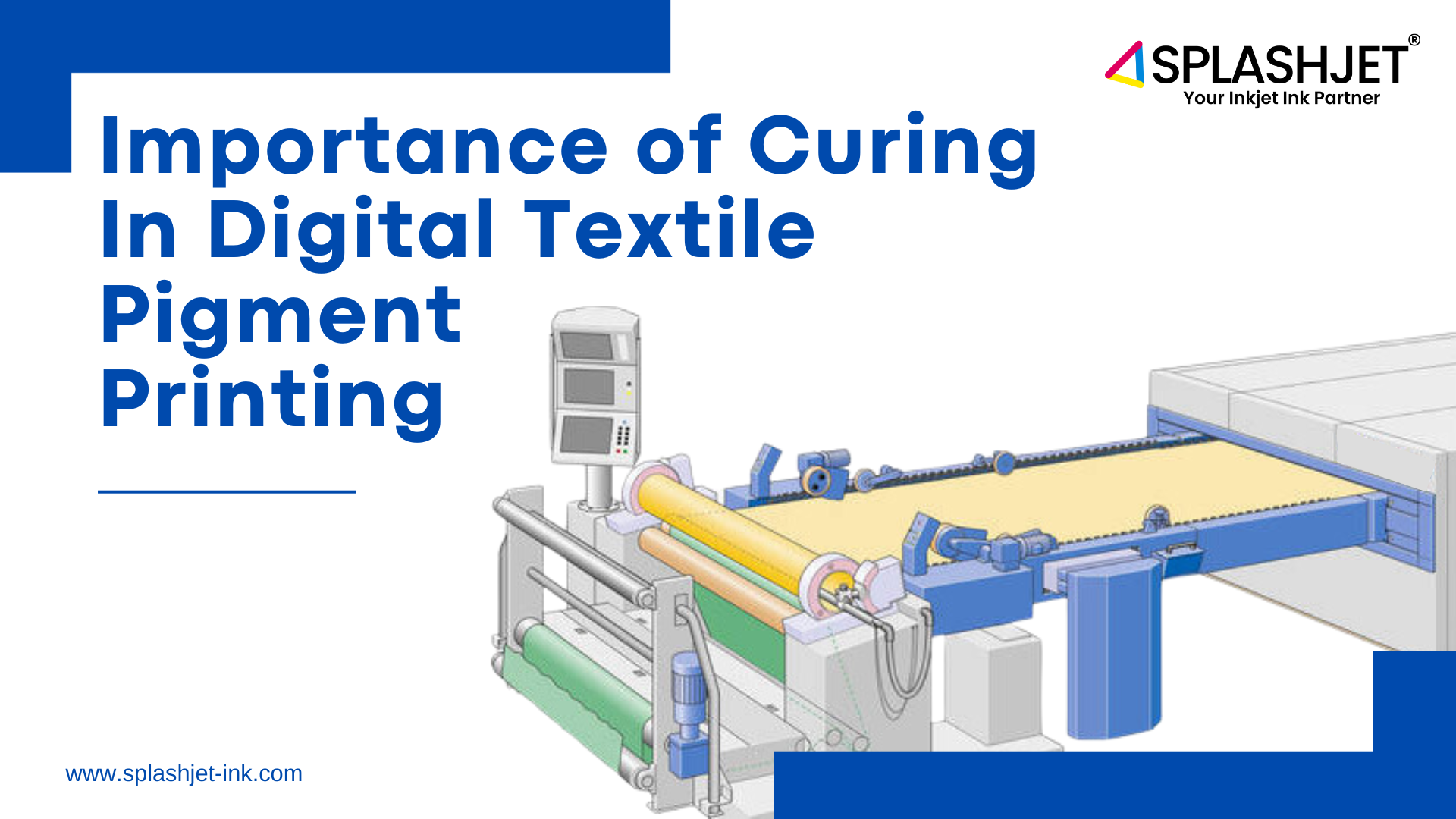
For years, those who have worked with digital textile pigment inks, have experienced the importance of curing and binder chemistry. Let’s understand the secrets behind the Curing in Digital Textile Pigment Printing.
The mechanism is simple: when the printed fabric is cured, a process called polymerization takes place. At the time of polymerization, the polymer binder in the ink polymerizes (melts in layman’s terms) and creates adhesion between the pigment particle and the fabric. Here, it is the quality of the binder that has an impact on the fastness of the fabric.
Before we dive into the mechanism of curing or fixation, let’s first understand the steps involved in digital textile pigment printing.
Digital Textile Pigment Printing Comprises 4 main sub-processes –
- Pre-Treatment
- Drying
- Printing
- Curing or Fixation
Importance of Curing in Digital Textile Printing:
Other than the binder chemistry of pigment inks, here are the most significant parameters that enhance the performance of your digitally printed fabric with pigment ink.
- Color Fixation: Curing helps fix the color of the pigment onto the fabric to prevent fading during regular washes.
- Durability: The cured ink becomes more resistant to physical stress, including washing.
- Adhesion: Curing ensures proper adhesion of the pigment particles to the textile fibers and prevents rubbing.
- Hand Feel: Proper curing of the printed fabric ensures a better hand feel due to the surface printing nature of pigment inks.
- Final Appearance: The curing process can influence the final appearance of the print, including the print’s glossiness and texture.
- Evaporation of Solvents: Pigment inks contain water or other solvents to keep the ink in a liquid state. The heat curing enables you to leave only solid pigment particles on the textile.
- Activation of Binders: Pigment inks typically contain binders or polymers that help fix the pigment particles onto the textile fibers.
Now let’s dive into the mechanism of curing and let’s discuss the most widely used techniques to perform the curing of digital textile pigment inks.
1. Calender Heat Press Machine –
where the fabric is pressed against two hot rollers which keep applying pressure and heat simultaneously to activate the binders.
- Pros – reliable, cost-effective, fast film formation on fabric, easy to use
- Cons – limited print size, heat, and pressure-sensitive, may affect the fabric texture if done with high pressure or temperature.
2. Stenter –
where the fabric is stretched over the continuous conveyor belt in an enclosed chamber with adjustable temperature and airflow to enable precise control with the help of clips or pins.
- Pros – high-quality curing, retains the texture of the fabric, ideal for continuous roll fabrics
- Cons – high initial investment, complex operation, high maintenance, more energy consumption
3. Heat Tunnel Machine/ Tunnel Dryer –
where the fabric is placed with a heated conveyor belt in a chamber for a specific duration and simultaneously allowed to activate the binders in the pigment ink to make a permanent bond with the fabric.
- Pros – cost-effective for small printing businesses, compact, easy to use, fast curing speeds, low energy consumption, good ventilation, ideal for garments
- Cons – limited print size, limited wash fastness
4. Infrared heater –
where the fabric is exposed to infrared radiation directly to activate binders inside the pigment ink to bond permanently with the fabric fibers.
- Pros – easy to handle, economical, targetted heating with faster curing times, compact, portable, reduced energy consumption, improved print quality, environmentally friendly as it emits no harmful gases
- Cons – less reliability, higher initial cost, temperature control complexity, uneven heating potential
From the above, we learned that every different mechanism comes with its pros and cons. So, always select the right technique depending on your business setup.
Conclusion:
In conclusion, we’ve discussed pigment ink science and the steps involved in digital textile pigment printing. In addition, we’ve discussed the role of curing in digital textile printing with various types of curing techniques. Whereas, performing the right curing technique can help you achieve quality print results and add substantial benefits to your printing business.
Want to know more about pigment ink? please visit.
Splashjet Inkjet Ink Private Limited
Phone: +91-9209-008-467
Email: info@splashjet-ink.com
References:
https://www.printsafari.com/blog/a-complete-guide-to-digital-printing-for-textiles/
https://www.linkedin.com/pulse/heres-process-make-your-digital-textile-printing-success-bansal/
https://www.youtube.com/watch?v=8yoI2vCa5vw