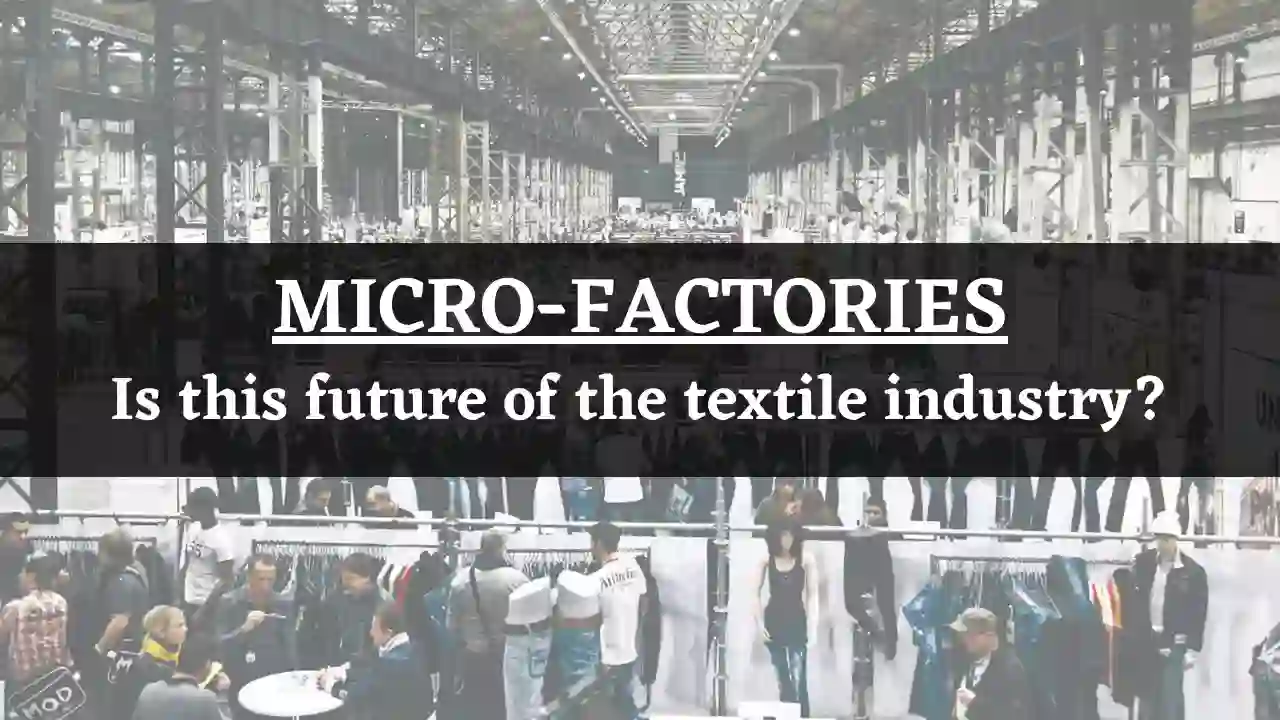
Introduction
If you’re familiar with the old-school manufacturing model where the textile products (for a variety of industries) were manufactured early in the process and held in stock before getting fed into the supply chain on a seasonal cycle, then you are well aware that changing business dynamics have made this model costly and risk-prone. This process requires a lot of inventory management and if the design does not sell, it’s either discounted or discarded in landfills.
The model puts considerable pressure on all ends of the supply chain. Growing costs of transportation, uncertainties of shipping availability, and fickle buying sentiment are the factors impacting the age-old business model. Is there any alternative to this model? That’s where the Microfactory comes in. Before we see what the “Micro-factory” really is, just a note that the traditional model will stay for bulk orders with its strong advantage of costs.
What is a micro-factory?
A micro-factory is an on-demand manufacturing business modal that reduces losses, every fashion business hopes, to increase sustainability and profits with a shorter manufacturing cycle.
How does the on-demand manufacturing work?
As we discussed earlier that the idle standard modal of fashion business involves 4 basic processes of manufacturing, i.e. designing, developing, making, and selling. However, the standard modal involves two additional auxiliary processes which decrease the business profits i.e. discounting and discarding.
The micro-factory concept reduces the last two auxiliary processes and flips the order of manufacturing the fabrics i.e.
- Design
- Develop
- Sell
- Make
In this process, the fabrics are made only after they are sold or when there is strong data-driven demand from the shop floor shelves, hence the wastage is reduced and business profits can be increased. This innovation in the fashion industry is named “Industry 4.0” and is described as the fourth industrial revolution.
Industry 4.0 and Individualization: the micro-factory in the field of textile printing
Industry 4.0 is a term used to describe the fourth industrial revolution. It is the integration of cyber-physical systems, cloud computing, and the Internet of Things (IoT) into manufacturing processes such as textile printing.
The combination of these technologies has allowed for new advances in quality control, robotization, and automation of manual operations, which in turn will help make production more efficient while lowering costs of production for companies.
The enabler behind all these innovations is the digitization of the Textile Industry. The Industry 4.0 green revolution is majorly dependent on advancements in the digital printing process.
Micro-factories are one way that Industry 4.0 can be implemented at scale by small businesses or individuals who want to benefit from this new paradigm without having access to large facilities or expensive equipment like those found at traditional factories.
What are the characteristics of the micro-factory?
- It is a flexible and resilient network.
- It can be deployed in any kind of environment, from small startups to large companies.
- The micro-factory is also an integrated procedure: it combines traditional textile printing with additive manufacturing technologies such as 3D designing and printing.
Benefits of Micro-factory
Fashion manufacturers in developed high-wage countries have lost business to larger-scale suppliers in lower-cost countries as a result of the globalization of fashion supply chains.
However, the trend toward digitization and mass customization means that micro-factories close to customers will be an important component in the future of fashion manufacturing, with benefits such as faster time-to-market, flexibility, and a lower carbon footprint.
Here are some more benefits of micro-factory in the Textile Industry –
- Greater opportunity for innovation
- Flexibility to shift between different product types
- Efficient management of smaller quantities
- Enhanced ability to tailor data-driven products at a lower cost.
- Reduce waste, especially natural resources such as water.
- Lower labor costs due to AI and automation
- Lower set-up and overheads cost
- Lower freight costs being closer to market
- Lower custom duty impacts and many more.
Integrated development procedure for individualized products
Industrial experts are developing a new process that will allow us to integrate the development of an individualized product with the creation of a virtual prototype. The result is a networked procedure that combines both functional and aesthetic aspects of textile printing in one step, thus enabling us to create products faster and more efficiently than ever before.
The technology involved in Integrated development
- Virtual prototype integration (pre-printing), which involves creating 3D models based on your original design;
- Networked procedure execution (post-printing), in which you can choose from various options for applying your design;
- Micro-factory production (production).
Future production will be possible according to the needs of the customer.
The micro-factory is an ideal platform for the future production of textile printing. Customers can now choose from a wide range of products and have them produced according to their needs. In this way, micro-factories can offer individualized products that are tailored to each client’s specific requirements.
As such, these factories will be able to offer flexible production: If a certain type of fabric becomes popular in one country but not another, then it would be possible for manufacturers in those markets (or even within countries) to adjust their output accordingly without having any impact on the whole supply chain or costing any extra money – just by changing how they use existing machinery and materials!
The future of textile printing is close at hand, with the micro-factory emerging as a key player in this process. This development will allow individualized products to be produced using smart materials and lightweight machines. It is also expected that virtual planning methods will become standard practice for creating production networks, allowing for quick and flexible responses to customer demands.
Our Take Away for Green Revolution
The advent of Industry 4.0 has allowed us to see more clearly just how complex these processes are; all of the essential elements of the Textile Micro factory, including software, textile printing inks, and machinery, are now available, providing the industry with the toolbox it requires to make the transition to sustainable manufacturing, it’s time we started thinking about them as a whole rather than piecemeal solutions.