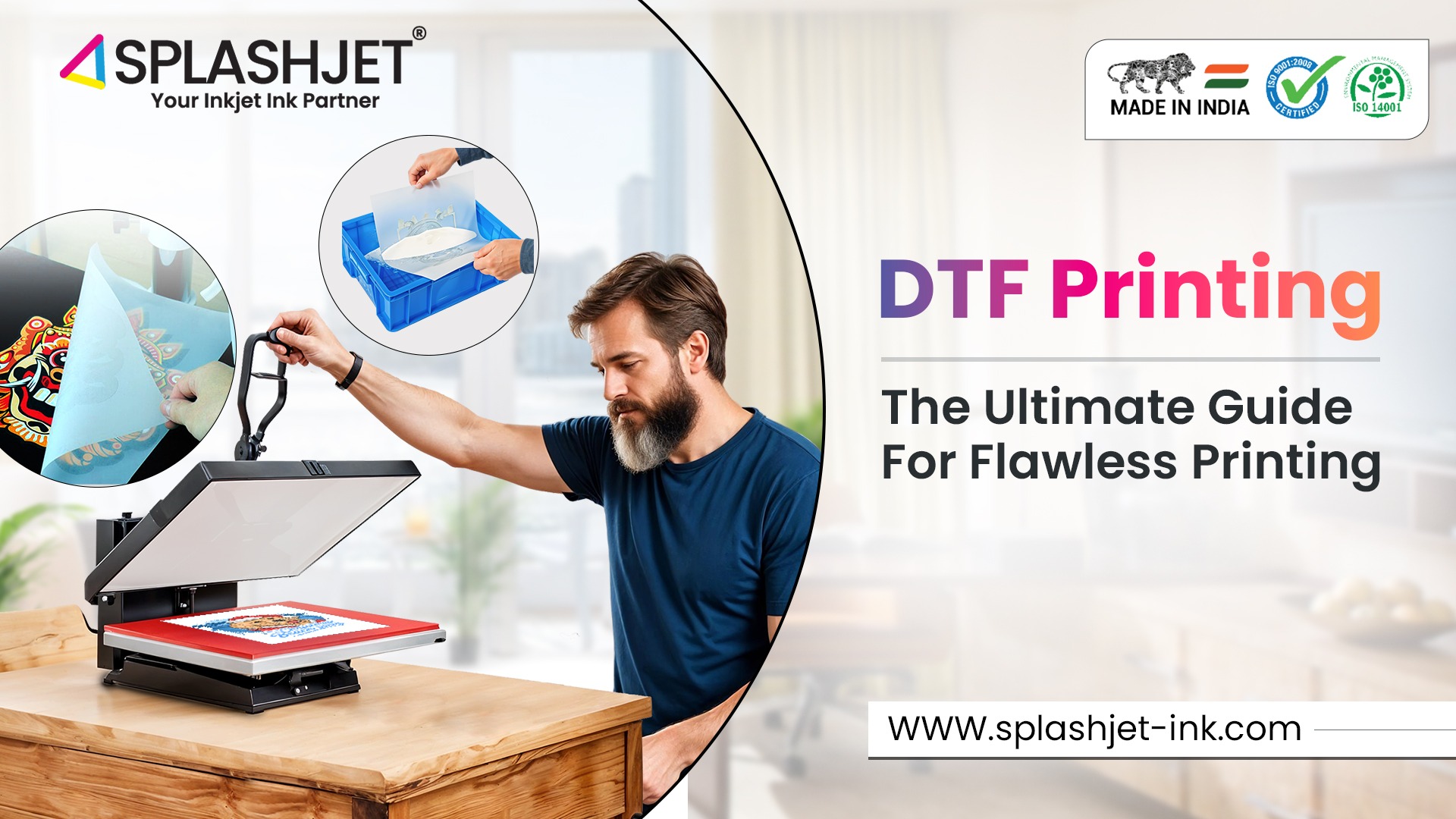
In the fast-paced fashion world, people often seek trendy, unique, and cost-effective styles. DTF offers a reliable solution to print custom designs on a variety of fabrics, including cotton, polyester, and polyblends. This ultimately helps printing businesses stay in sync with changing trends and meet market demands.
This raises a solid and striking question: What factors affect the print Results? Most importantly, what are the major actions that can be taken to make the DTF prints outshine the rest? Let’s list down them one by one
Important Factors to Be Taken Care Of
DTF Printing results can be diversely affected by the factors mentioned above, let’s have a glance at what makes these factors a major concern
A. Printhead Condition
If the printhead is not regularly maintained or cleaned, it may result in inconsistent prints and clogging issues. This is especially true with white inks, which have larger particles and require more frequent attention to prevent clogging problems
B. DTF Transfer Films
It is important to ensure the film is properly placed on the fabric, assess its coating type, and verify compatibility with your inks; otherwise, you may encounter poor results.
C. Hot Melt Powder
The hot melt powder plays a crucial role in ensuring adhesion between the fabric and the print. Two key factors that may affect print quality are the particle size and the melting point of the powder. Proper attention to these factors can prevent uneven adhesion, clumping, and ensure excellent color vibrancy.
D. Operating Conditions
Controlling moisture, temperature, and humidity in the printing environment is crucial for enhancing print performance and ensuring consistent, high-quality results.
E. Color Management Process
This involves color profiling, correction, and matching to achieve the desired quality. Using ICC profiles ensures optimal color reproduction and minimizes color accuracy issues. Creating and testing custom ICC profiles with different DTF film combinations enables accurate color reproduction, vibrant prints, and consistent performance.
We’ve covered the factors that can mess up your prints, now let’s look at the things you can do to boost your printing results and get consistent, high-quality DTF prints.
Best Practices to ensure your DTF prints stand out
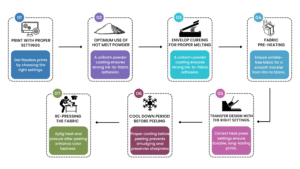
Step 1: Print with Proper Settings
Choose the correct print settings to ensure flawless results. Make sure you select the right printer settings and verify the design dimensions to avoid any issues during the transfer process.
Step 2: Use Hot Melt Powder Optimally
Use hot melt powder correctly to ensure strong ink-to-fabric adhesion. This improves durability, vibrancy, and overall print quality.
Step 3: Envelop Curing for Proper Melting
Proper melting of hot melt powder is crucial. It ensures even adhesion across the transfer area and prevents clumps, which can affect vibrancy and ink-to-fabric adhesion
Step 4: Fabric Pre-heating
Ensure the fabric is free of wrinkles before transferring the design. Wrinkles can result in uneven printing, so prepare a smooth surface for a flawless transfer from film to fabric.
Step 5: Transfer Designs with Proper Heat Press Settings
Setting the correct temperature and time is critical for heat pressing. Incorrect settings can burn the fabric and cause yellowing or scorching.
Settings | Recommended Value |
---|---|
Temperature | 180°C- 210°C |
Time | 10 sec- 60 sec |
Pressure | Moderate |
Disclaimer: It is recommended to check the settings with your heat press machine manufacturer, as they may vary from machine to machine for optimal results.
Step 6: Cool Down Period Before Peeling
Allow sufficient cooling time before peeling off the film. This prevents smudging and maintains the sharpness and clarity of your design. The cooling time may vary depending on the type of film you use.
Step 7: Re-Pressing the Fabric
If you notice moisture issues or want to improve color fastness, re-press the fabric. Applying heat and pressure helps remove excess moisture, enhancing the vibrancy and durability of your design.
Conclusion:
By analyzing and addressing the factors that can compromise print quality, and optimizing your processes, you can significantly reduce the chances of print damage. Adopting and following these best practices will help you achieve excellent results in your DTF printing, boosting your business, and enabling you to meet customer demands and expectations in the fast-paced fashion world.