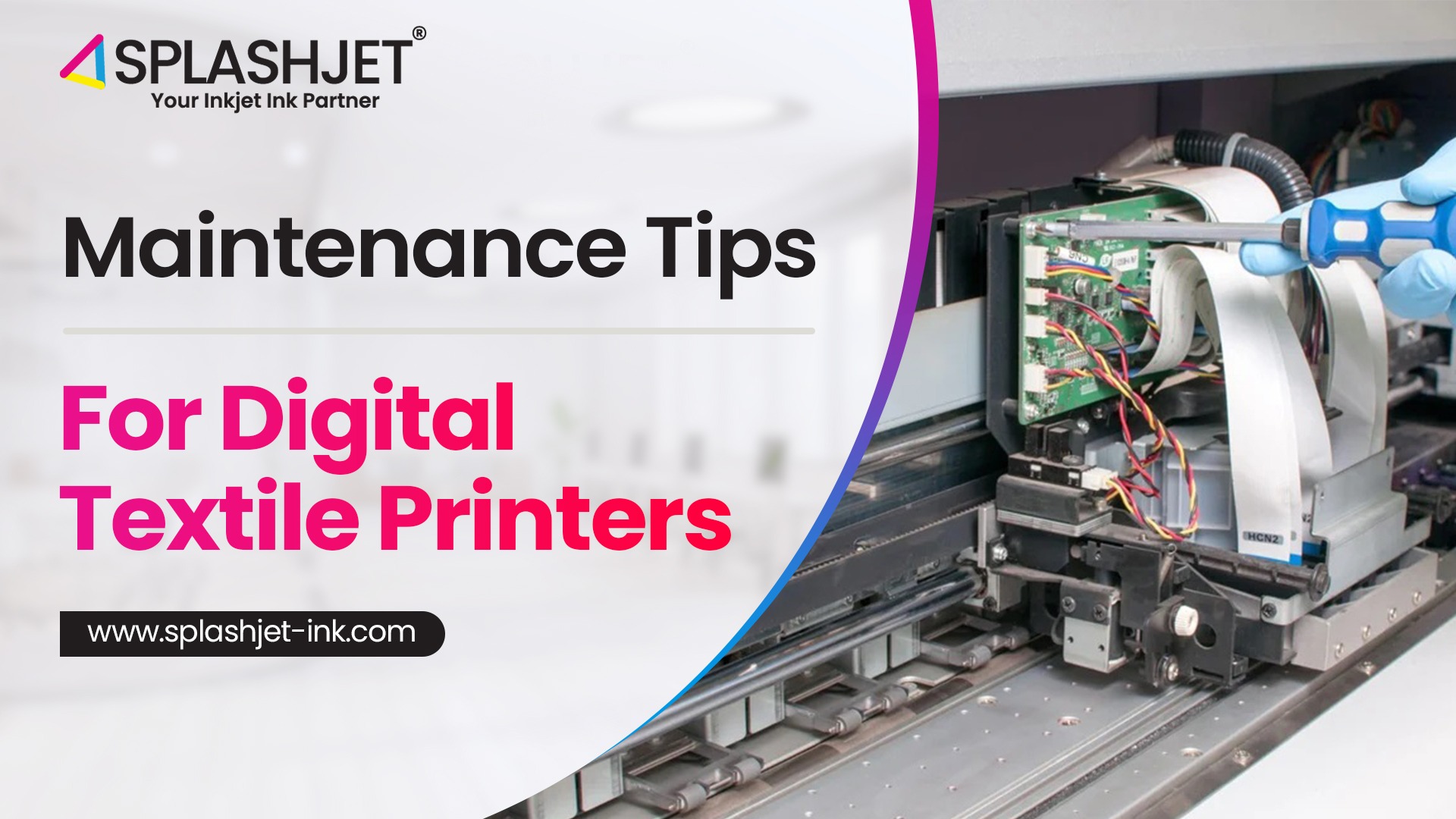
Have you ever wondered why unexpected breakdowns occur with textile printers, leading to increased downtime and costly repairs? Maintaining your textile printer isn’t just about keeping it operational; it also involves proper printer maintenance. Ignoring regular maintenance can lead to nozzle clogs, printhead damage, and poor print quality. In this article, we will guide you through 5 tips for textile printer maintenance which will minimize your printer downtime, eliminate costly repairs, and ensure consistent print quality.
1. Regular Cleaning
Daily, and periodic maintenance can prevent costly repairs and ensure your printer runs smoothly. Let’s see how your little efforts can save you from major breakdowns.
Maintenance Frequency | Tasks | Notes |
---|---|---|
Daily Maintenance | Remove dust from the external surfaces of the printer | It can affect print quality in the long term. |
Run a nozzle test before and after printing | For consistent print |
|
Periodic Maintenance | Clean the printhead with a recommended solution | To remove ink debris, clogs |
Clean the rollers | Avoid fabric damaged | |
Clean the capping station to remove ink debris | To avoid nozzle clogs & printhead damage | |
Clean and replace the wiper blade regularly | To remove dust and excess particles | |
Clean encoder strip and paper guide | To maintain the correct position of the printhead for a smooth color |
Note: Add 1–2 ml of cleaning solution to the capping station, especially when using white ink for DTF textile printers. If you are not using white ink, this step can be skipped.
2. Ink Management for textile printers
- Always use original or high-quality compatible ink to ensure reliable performance.
- Maintain ink levels above 25%–30%. Low ink levels can cause ink interruption resulting in slow printing with faded prints.
- Keep ink in a cool, dry, and sealed container. For best performance, use it within two months of opening.
- Avoid exposing the ink to direct sunlight, as it may alter its composition.
3. Proper Media Handling for Textile Printers
Proper media handling is an essential aspect of textile printing. Damaged paper roll edges, lint on fabric, or unfinished edges can obstruct printhead nozzles, leading to defects. Additionally, low ink limits and dust accumulation affect ink absorption capacity, reducing printer productivity and lifespan. Regular maintenance, such as replacing ink filters and dampers quarterly, helps ensure smooth operation.
Keeping the printing environment clean minimizes dust-related issues, enhancing print quality. Properly storing and handling media prevents physical damage and maintains consistency in prints. Following these best practices extends printer life and improves overall efficiency in textile printing.
Conclusion
Practicing these routine maintenance tips can significantly reduce your printer’s downtime and the need for costly repairs. Regular attention to ink levels, the capping station, and the wiper blade are essential for ensuring optimal performance and longevity. Additionally, it’s important to know when to seek professional help for your printer. By combining routine maintenance with expert support, you can extend your printer’s lifespan, improve print quality, and minimize downtime.